
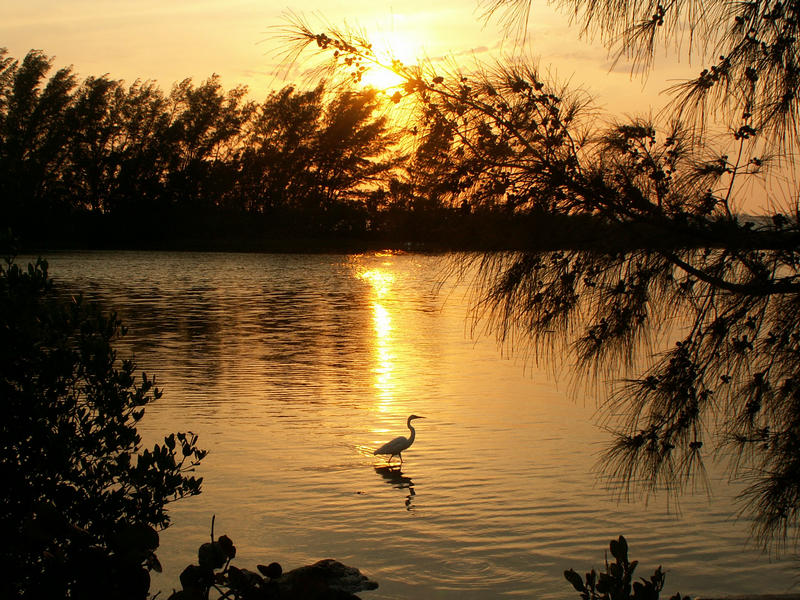
SOP - 12. Site Visits and Inspections
- Home
- Divisions
- Division of Waste Management
- Petroleum Restoration Program
- SOP - 12. Site Visits and Inspections
Petroleum-Restoration Quick links
- Petroleum Restoration Program
- PRP Contacts
- Announcements & Upcoming Events
- Administrative Guidance
- Agency Term Contracts (ATC)
- Assessment Guidance
- Competitive Procurement System
- Database Reports & Site Files
- General Technical Guidance
- Innovative Technology Acceptance Program
- Monthly Dashboard Update
- Petroleum Cleanup Programs
- Presentations & Brochures
- Priority Score Funding Threshold History
- Procedures & Guidance Documents
- Qualified Contractor Information
- Related Links
- Remediation Guidance
- Rules and Statutes
- SOP
- Templates, Forms, Tools and Guidance
- Webpage Updates History
- Weekly Encumbrance Approval
- All Petroleum-Restoration content
Site Visits
Purpose of Site Visits
Site Managers (SM) visit sites to gain an understanding of site‑specific conditions including logistics and constraints that may affect the petroleum cleanup work at a site. Site visits help a SM gain a better understanding of fieldwork methods and equipment used and to learn more cost‑effective methods of accomplishing work at the sites they oversee. SMs are not limited to visiting their assigned sites; they can also coordinate visits to sites assigned to other SMs.
Ideally, site visits should be scheduled when the contractor is performing work at the site. However, site visits are also useful for the following purposes:
- Conducting a site walk-over to observe and document current site conditions including source area locations, monitoring well locations, buildings and structures, traffic, right-of-ways and other logistical concerns.
- Confirming previous work performed at the site.
- Conducting on site meetings with a site owner, operator, contractor or subcontractor to discuss the field work and concerns the parties may have.
Notifications
The Owner/RP or tenant/operator should be contacted when scheduling a site visit. If fieldwork will be occurring during a planned site visit, the SM may want to coordinate with the Contractor.
Contractors are required to notify the SM and the site owner/operator of scheduled field work at least seven calendar days prior to conducting on-site field activities in accordance with the Specifications of the purchase order Attachment A - Scope of Work.
Office Preparation
Before a SM travels to a site, permission to travel which may include a Travel Authorization form must be approved. In addition, the SM should gather pertinent information that will assist with conducting the site visit. This includes, but is not limited to, the following:
- Site Inspection Form (see below);
- Personal Protective Equipment (see Health & Safety below);
- Cell phone/camera;
- Work Plan/Scope of Work (if observing field work); and
- Maps or Figures: current site map/vicinity, map/contaminant plume, maps/elevation contour map.
- Tabulated data if available: Soil and Groundwater Analytical Tables, Groundwater Elevation Tables.
Health & Safety
SMs are observers and do not actively participate in field work. Site control is maintained by the contractor performing the work and is not the responsibility of the SM. If the site is visited during field activities, SMs should note designated work zones or exclusion zones and request to see the Contractor’s Health and Safety Plan (HASP). Signing the HASP is not a requirement for a SM.
OSHA Requirements
- As observers, SMs must have a minimum of 24 hours of OSHA health and safety training. Many have the full 40-hour OSHA training. An annual eight-hour refresher course is required to keep this training current.
Personal Protective Equipment (PPE)
- SMs must wear appropriate PPE during site visits when work is performed. This includes hardhat, safety glasses and earplugs. Appropriate attire includes long pants and comfortable shirt. Steel‑toed shoes and safety vest are recommended. Water, sunscreen and bug spray may also be warranted.
Traffic Control
- SMs should always be observant of the flow of traffic when conducting a site visit, particularly if visiting an active service station. SMs should make note of the contractor's traffic-control measures with respect to the work zones.
Site Inspection Form
Site Managers shall complete a Site Inspection Form for every site visit they make. A new Site Inspection Form is required to be filled out even if there are several site visits for the same site. The form is designed to be filled in with basic site information before the SM leaves for the field.
Site Visit/Inspection
Always check in with the site owner or facility operator upon arrival to the site.
If the purpose of the site visit is to conduct a site walkover, note the following:
- Confirm locations of on-site gasoline or petroleum product tanks and dispensers;
- Identify buildings, structures and aboveground utilities located on site;
- Note location and condition of remedial system equipment compound, if applicable;
- Confirm apparent property boundaries and right-of-way;
- Confirm monitoring well or soil boring locations;
- Take photographs, both general view and close-up shots, from all four compass directions for buildings, canopies, driveways, sidewalks, landscaping, etc., and any visible specific pre-existing damage or issues noted in the description; and
- Record observations.
If observing field work during the site visit:
- Review the scope of work prior to arrival;
- Check in with the contractor’s on-site supervisor when it is safe to do so;
- Make note of the contractor’s staff and any subcontractors working on-site;
- Identify designated work areas and staging areas. Note where contaminated soil and groundwater are being removed, discharged, containerized or stockpiled;
- Observe activities from a safe distance and record observations in field notebook or on the inspection form;
- Take relevant photos; and
- Note any observed health and safety issues.
Upon return to the office, finalize the inspection form and attach relevant photos for upload to OCULUS. Discuss findings with PE or PG or the consultant as needed.
Inspector Program
The PRP utilizes dedicated inspectors to monitor work performed at state-funded sites. In general, contracted Local Programs are responsible for inspections at sites they manage within their respective geographic areas, while Teams 5 and 6 are responsible for inspecting sites managed by Tallahassee program staff. Overall, site inspections help to provide accountability and document that trust fund cleanup dollars are appropriately spent.
The two general categories of site inspections are described below.
Field Inspections
Field Inspections provide documentation of site conditions and the field work performed by state contractors. Field Inspectors are observers only and do not direct the contractors performing the work. Field Inspectors observe activities common to petroleum cleanup work including groundwater sampling, well construction, soil sampling, SRs, RAC and other activities. Field inspectors provide several important benefits to the petroleum program, including:
- Confirmation that the scope of work is completed as required in the PO or WO.
- Confirmation of field methods used and contractor’s conformance with established SOPs and guidelines.
- Provide real-time feedback of work progress to the site managers and technical reviewers, and confirm logistical problems and necessary changes in SOW.
- Document personnel, equipment, and subcontractors mobilized to a site for approval of payment.
- Provide photographic documentation of baseline site conditions, site restoration and work in progress.
- Document that contractors have a HASP available for viewing when work is performed. Emergency contact information, route to hospital and sign-in sheet must be onsite in paper format.
O&M Inspections
O&M Inspections involve all aspects of remedial systems including system startup and routine operation and maintenance. The O&M Inspector documents operational status of remedial systems including system parameters and operating efficiencies. Inspections are completed with and without contractors present at the site. Inspectors do not make system adjustments or repairs to equipment.
O&M inspections can include, but are not limited to, the following:
- Confirmation of system “Run times” and reasons for system downtime.
- Review of maintenance history and whether it was performed in accordance with the manufacturer’s specifications.
- Verify that remediation system components are installed in accordance with the approved RAP or RAP Mod and the as-built drawings.
- Verify that the system equipment and components are operating properly, and record all observations and system performance parameter measurements at the equipment, manifolds and wellheads/treatment points, as applicable
- Verify that the remediation system performance measurement devices are installed in accordance with the approved RAP/RAP Modification and that they are operable and capable of measuring the required parameters, including hour meters, electric meters, flow meters and totalizers, pressure gauges, vacuum gauges, liquid level indicators, etc.
- Verify that the critical fail-safe/interlock mechanisms are installed in accordance with the approved RAP/RAP Modification and ask the contractor to demonstrate that they are functioning properly, where possible. Examples include high liquid level sensor/cutoff, high pressure sensor/cutoff, air sparge shut off if VES fails, low oil level sensor/shut off, high temp sensor/cut off, power supply monitor/cut off, etc.
- Observe and record general site conditions and any factors affecting site safety or cleanup efficiency.
- Conduct state-owned equipment inventory verification for program SMs and inventory coordinators.
Scheduling Inspections
Inspections at petroleum cleanup sites are scheduled based on field work notifications from contractors and requests from program staff as follows:
- Field work notification from the contractors: Contractors are required to send notification of scheduled field work to the centralized e-mail address, prp_inspector@floridadep.gov in addition to the site manager at least seven calendar days prior to conducting on-site field activities. The scheduling coordinators and inspectors monitor the field notifications that are submitted in order to develop inspection schedules.
- Direct request from program staff: For Tallahassee program staff, requests can be made to the scheduling coordinator or Team Leader for Teams 5 and 6. local Programs have internal inspectors and requests should be handled internally. Requests should include the basic information used for field notifications along with the specific reason for the request and any expectations they have for the inspection. For complex or lengthy projects, requests can be made for regular visits to the site for the duration of the project.
Coordinators and Inspectors typically develop a weekly schedule in a logical and efficient manner focusing on geographic areas of the state. Schedules are adjusted during the week based on actual field work being performed and any additional site inspection requests. The frequency and specific scope of any given inspection is determined by the inspector, coordinator and the PRP Team making the request.
Inspection Reports and Communication
Inspectors contact the assigned SM during the inspection to provide feedback and make SMs aware of important observations including changes to the SOW. Inspectors can also facilitate coordination and communication between a SM and field supervisor if problems or issues arise.
For O&M inspections, a post-inspection meeting between inspector, SM, and PE can be coordinated to discuss the inspection findings and operational data observed.
Field inspectors and O&M inspectors utilize different standardized report templates optimized for the type of inspection. Inspection reports are completed by the inspectors either in real time or upon return to the office or hotel. Copies of reports are uploaded to OCULUS (Profile: Discovery_Compliance; Document Type: Inspection Related) and emailed to the SMs. Site managers should carefully read the inspection reports and confirm if there is anything that requires follow-up discussion with the contractor or within their team or section. Site managers are encouraged to contact the inspector if they have questions about the information presented in the inspection report.
Return to: PRP Site Manager Standard Operating Procedures (SOP) webpage.
Interested in subscribing to DEP newsletters or receiving DEP updates through email?
Sign UpAbout DEP
The Florida Department of Environmental Protection is the state’s lead agency for environmental management and stewardship – protecting our air, water and land. The vision of the Florida Department of Environmental Protection is to create strong community partnerships, safeguard Florida’s natural resources and enhance its ecosystems.
Learn MoreContact
3900 Commonwealth BoulevardTallahassee, Florida 32399-3000 Public.Services@FloridaDEP.gov 850-245-2118
